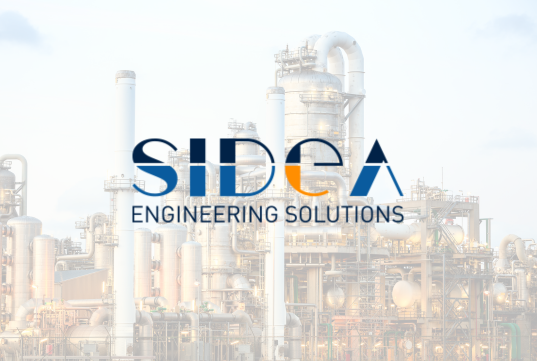
Industrial automation and supervisory systems: what do you know about SCADA systems
Chemical plants supervisory, automation and control systems, also known as Supervisory Control and Data Acquisition (SCADA) systems or Distributed Control Systems (DCS), are essential in the chemical industry to monitor, control and optimize chemical processes efficiently and safely. But how do they work and what are their main functions?
Chemical plants supervisory systems: what they are and what they are used for
Supervisory, automation and control systems for chemical plants are critical to ensuring operational efficiency, safety and regulatory compliance in the chemical industry. These systems integrate hardware and software to ensure the reliable operation of chemical plants, as well as helping to improve the quality of chemical products and reduce overall operating costs. Specifically, chemical plant supervision, automation, and control systems are industrial automation solutions that enable centralized monitoring, control, and data acquisition from chemical processes. This is through:
- Process monitoring: These systems continuously monitor critical parameters of chemical processes, such as temperature, pressure, flow rate, level, chemical concentration and more. Readings from sensors are collected and displayed in real time.
- Process control: Automatic control systems adjust field devices, such as valves, pumps and motors, based on sensor readings to keep process parameters within predetermined limits. This ensures that the process remains stable and meets production specifications.
- Alarms and notifications: SCADA systems generate real-time alarms when emergencies or situations outside the normal operation of the process are detected. These alarms are generally classified by severity and are notified to operators for immediate action.
- Data archiving: Process data are recorded and archived for analysis, long-term monitoring and regulatory compliance purposes. This data can be used to analyze past performance and plan improvements.
- Remote control: In some cases, automation systems allow remote control of chemical plants, which can be useful for remote monitoring and intervention.
- Process optimization: The data collected can be used to optimize chemical processes, improving efficiency, reducing energy costs and minimizing waste.
Supervisory, automation and control systems for chemical plants also include safety features that protect plants from dangerous situations, helping companies in adhering to regulations and safety guidelines. The operator interface offered by SCADA systems is intuitive and allows operators to monitor and control processes in real time with state-of-the-art graphical displays that visually represent process status.
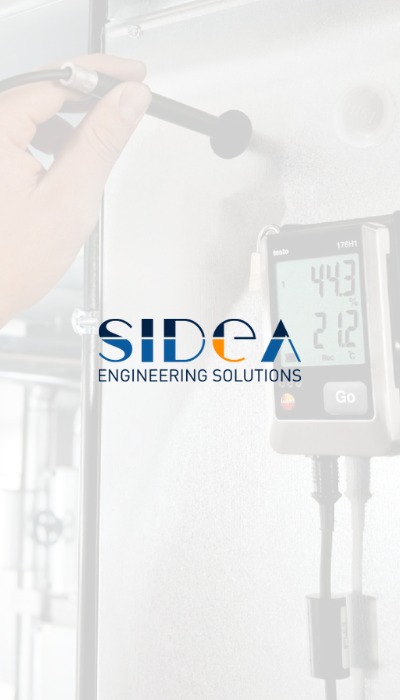
Supervisory systems for chemical plants: how do they work?
Key tools in the automation and control of chemical processes, helping to ensure operational efficiency, safety and regulatory compliance, SCADA systems are used in a wide range of applications, from chemical manufacturing to the pharmaceutical industry and water treatment, to accurately monitor and manage complex chemical processes.
But how does a SCADA system work?
Let's take a look together at the stages of operation of a SCADA system for chemical plants:
- Data collection from sensors and field devices: The SCADA system connects to sensors and field devices installed in the chemical plant. These sensors measure a wide range of parameters, including temperature, pressure, flow, level, chemical concentration and other critical process data. The data collected by the sensors are transmitted to the SCADA system.
- Communication: The SCADA system uses communication protocols to collect data from field devices. These protocols may vary by device type, but often include standards such as Modbus, OPC (OLE for Process Control), or custom protocols.
- Data processing: Once acquired, data are processed by the SCADA system to generate understandable information. This may include diagnostic calculations, unit conversion, and other data processing.
- Real-time visualization: Processed data are displayed in real time on user interface screens. Operators and control personnel can monitor the operation of the chemical process through graphical screens showing process diagrams, indicators, graphs, and tables with real-time data.
- Process control: The SCADA system allows operators to perform process control, often in automatic or manual mode. They can open or close valves, start or stop pumps, adjust temperature and other process variables directly from the SCADA interface.
- Alarms and notifications: The SCADA system can generate alarms when emergencies or situations outside the norm are detected. These alarms are generally classified according to severity and are notified to operators through visual, audible signals or digital notifications.
- Data archiving: Historical data are archived on storage media, often in database form, for purposes of historical analysis, long-term monitoring, and regulatory compliance. This data can be retrieved at any time for post-event analysis or research purposes.
- Reports and analysis: The SCADA system can generate periodic or on-demand reports based on the historical data collected. These reports can be used for performance analysis and chemical process improvement.
- Security and controlled access: SCADA systems implement security measures to protect access to data and control functions. Authorized users have access only to functions and data relevant to their role.
SIDeA: by each customer's side with supervisory system design and development solutions for chemical plants
From analyzing and understanding the problem, evaluating the feasibility of interventions, each customer is followed and supported by SIDeA engineers during each phase. When designing supervision systems for chemical plants and their subsequent development, SIDeA's commitment does not end with the delivery of the required solutions. In fact, the phase following implementation is that of training, as well as technical support, tutoring, assistance and maintenance to optimize the systems and their use by the customer himself.
A heterogeneous and flexible work team, capable of managing the workload based on the professionalism and skills of each collaborator, guarantees a production flow that can carefully and accurately meet the established delivery deadlines.