SIDeA Srl was founded in 1990. In over thirty years of activity, SIDeA has acquired the technological experience needed to develop quality solutions, offering consultancy and support services for the complete satisfaction of its users. SIDeA designs, develops and distributes solutions to ensure the correct execution of key processes in multiple applications, in industry and research.
A modern space in which to welcome customers and an organized, functional and professional work environment, allows SIDeA to follow the Customer in each phase, from design to realization, of every idea thanks to a solid experience in the field of systems and electrical engineering with a team of professionals able to satisfy your every need.
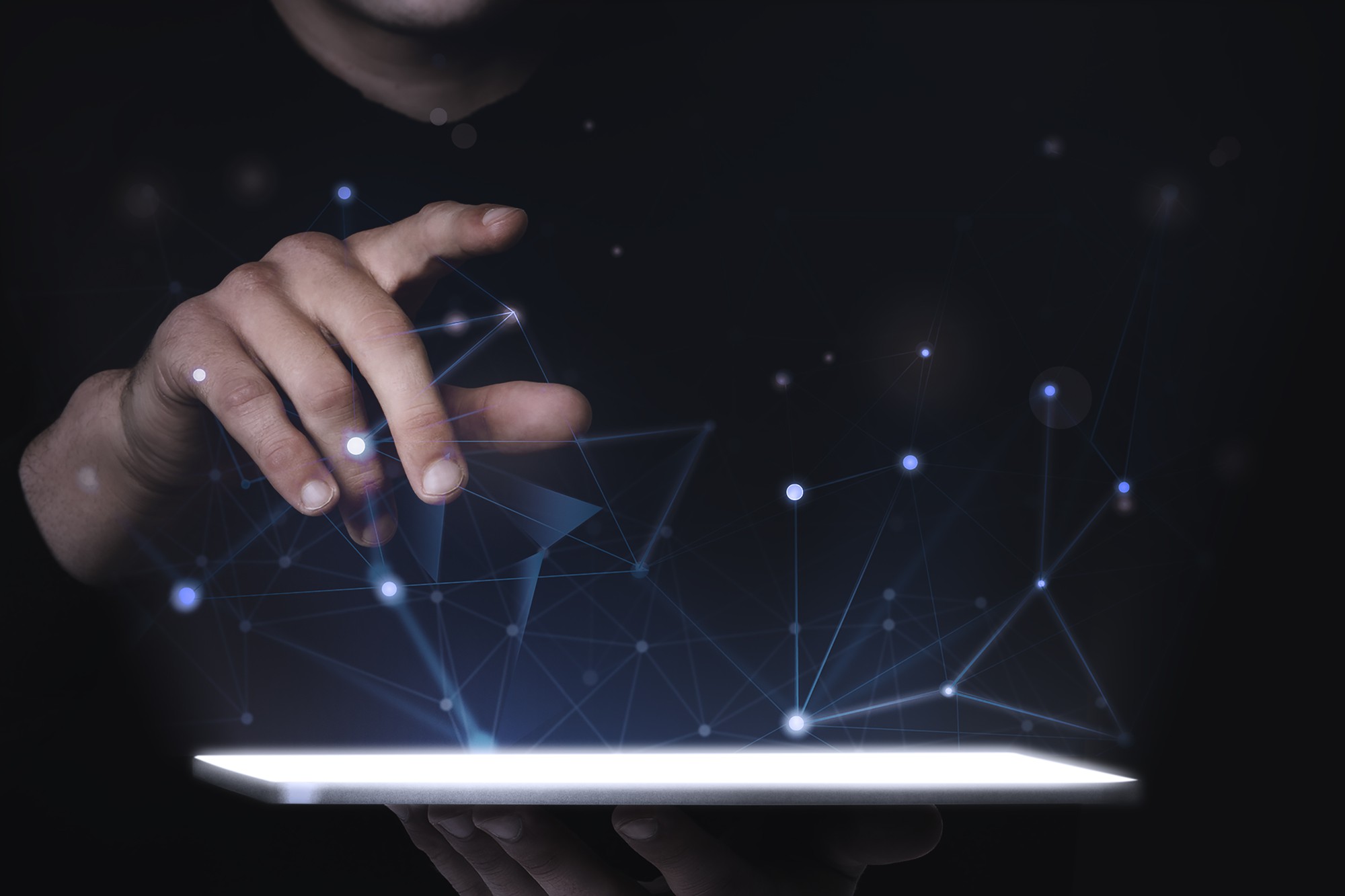
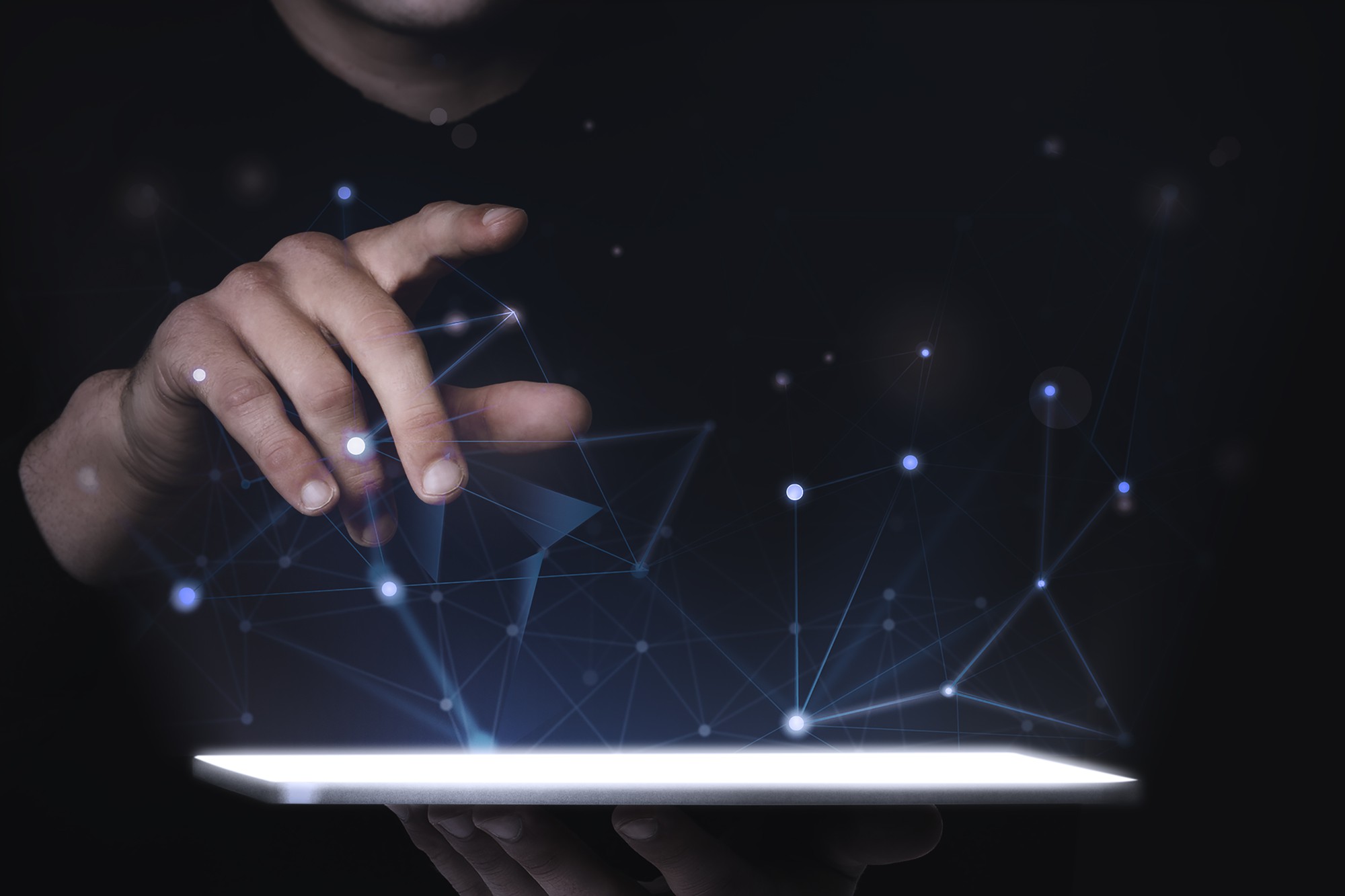
SIDeA Srl was founded in 1990. In over thirty years of activity, SIDeA has acquired the technological experience needed to develop quality solutions, offering consultancy and support services for the complete satisfaction of its users. SIDeA designs, develops and distributes solutions to ensure the correct execution of key processes in multiple applications, in industry and research.
A modern space in which to welcome customers and an organized, functional and professional work environment, allows SIDeA to follow the Customer in each phase, from design to realization, of every idea thanks to a solid experience in the field of systems and electrical engineering with a team of professionals able to satisfy your every need.
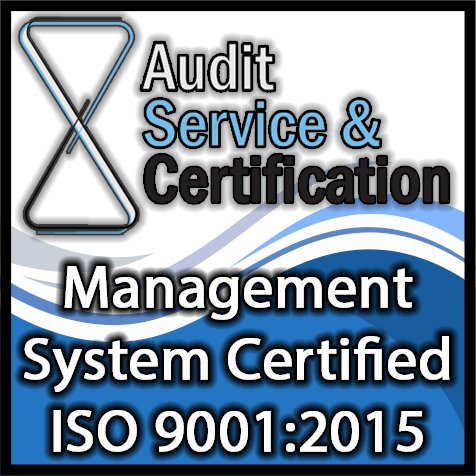
SIDeA Srl is committed every day to provide its customers with a wide range of services that can fully satisfy all their needs.
Through proven experience and expertise, research and development of cutting-edge services, commitment, punctuality and safety, the solutions offered always aim to meet the highest standards in terms of innovation, enhancement and development.
Always in line with the indications of specific regulatory bodies and with a view to excellence in the field of software, hardware, innovation and automation, SIDeA uses the most modern techniques and the latest generation software and hardware tools.
The objective that we intend to pursue and guarantee over time is the ever-increasing satisfaction of the Customer and to achieve it we have set ourselves the task of improving our business, our organization and our services by adopting a Quality Management System according to the principles established by UNI EN ISO 9001:2015.