The applications developed by SIDeA in the field of industrial automation cover a wide range of expertise across various sectors.
Among the topics addressed by SIDeA during its activities are:
The control systems developed integrate devices such as PLCs, data acquisition cards, and industrial regulators at various levels of complexity.
Supervisory control in the context of industrial automation and SCADA (Supervisory Control And Data Acquisition) are aimed at process control at the plant level.
The central elements of supervisory control systems are:
These elements includes a wide range of controls referring to both centralized and distributed architectures, referred to as DCS Distributed Control Systems.
A SCADA system is a monitoring and control system used in a variety of industries, such as energy, water, gas, and manufacturing. SIDeA develops custom SCADA systems designed to acquire, monitor, and control real-time data from devices and sensors distributed in contexts ranging from medium-sized installations to very large geographic areas.
The user interface allows for graphical visualization of information about industrial processes, such as production flow, temperature, and pressure, using a communication network to transmit data collected from devices and sensors to a central control system on a scheduled basis or upon variation. Data is stored in databases to enable trend analysis over time or alarm management.
In the same field, SIDeA designs and develops MES Systems (Manufacturing Execution System), which primarily monitor, control, and manage production operations within a company.
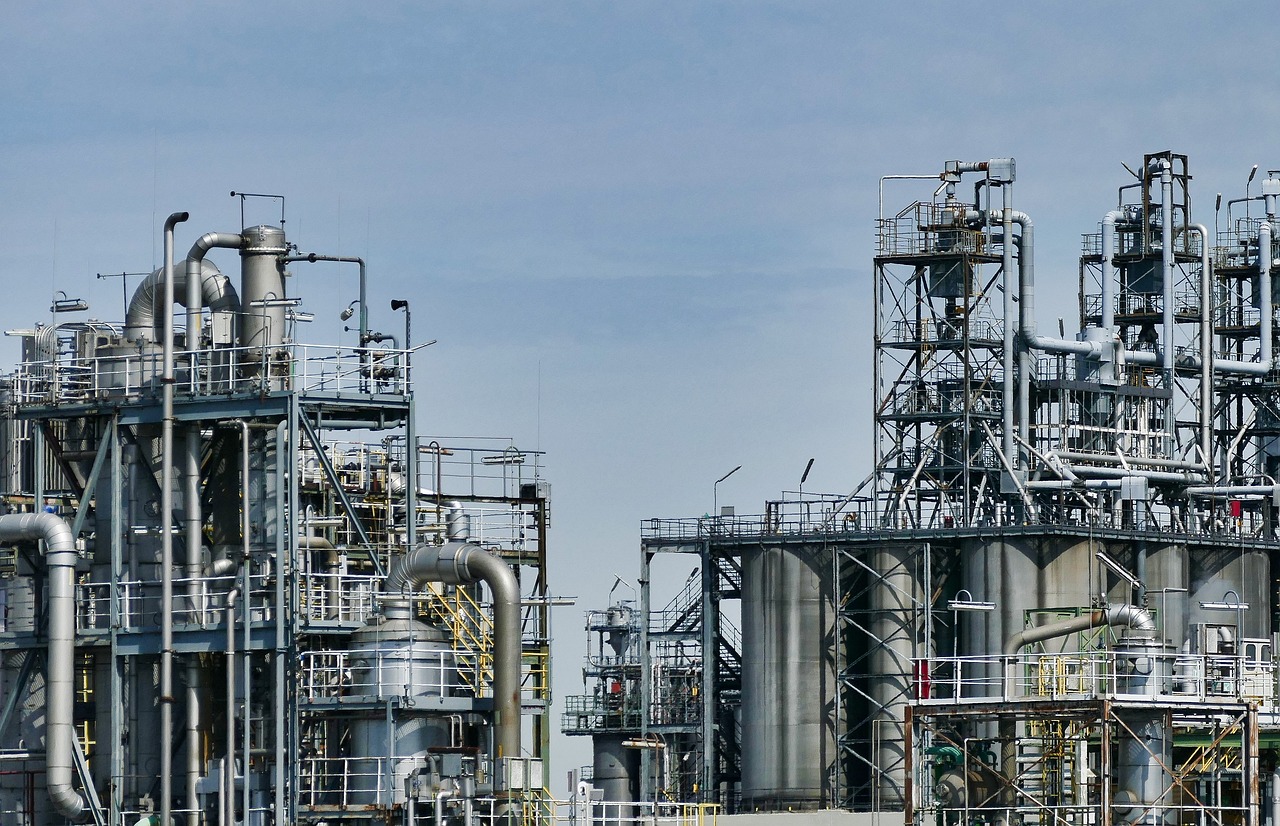
Chemical Plant Supervisory Control Systems
Supervision, automation, and control systems for chemical plants are used to monitor, control, and automate production processes, ensuring safety, efficiency, and reliability.
In the field of automation and control systems for chemical plants, SIDeA offers turnkey solutions through a wide range of technologies, including:
These components are interconnected to monitor and control production processes, from mixing and reaction processes to separation and purification operations.
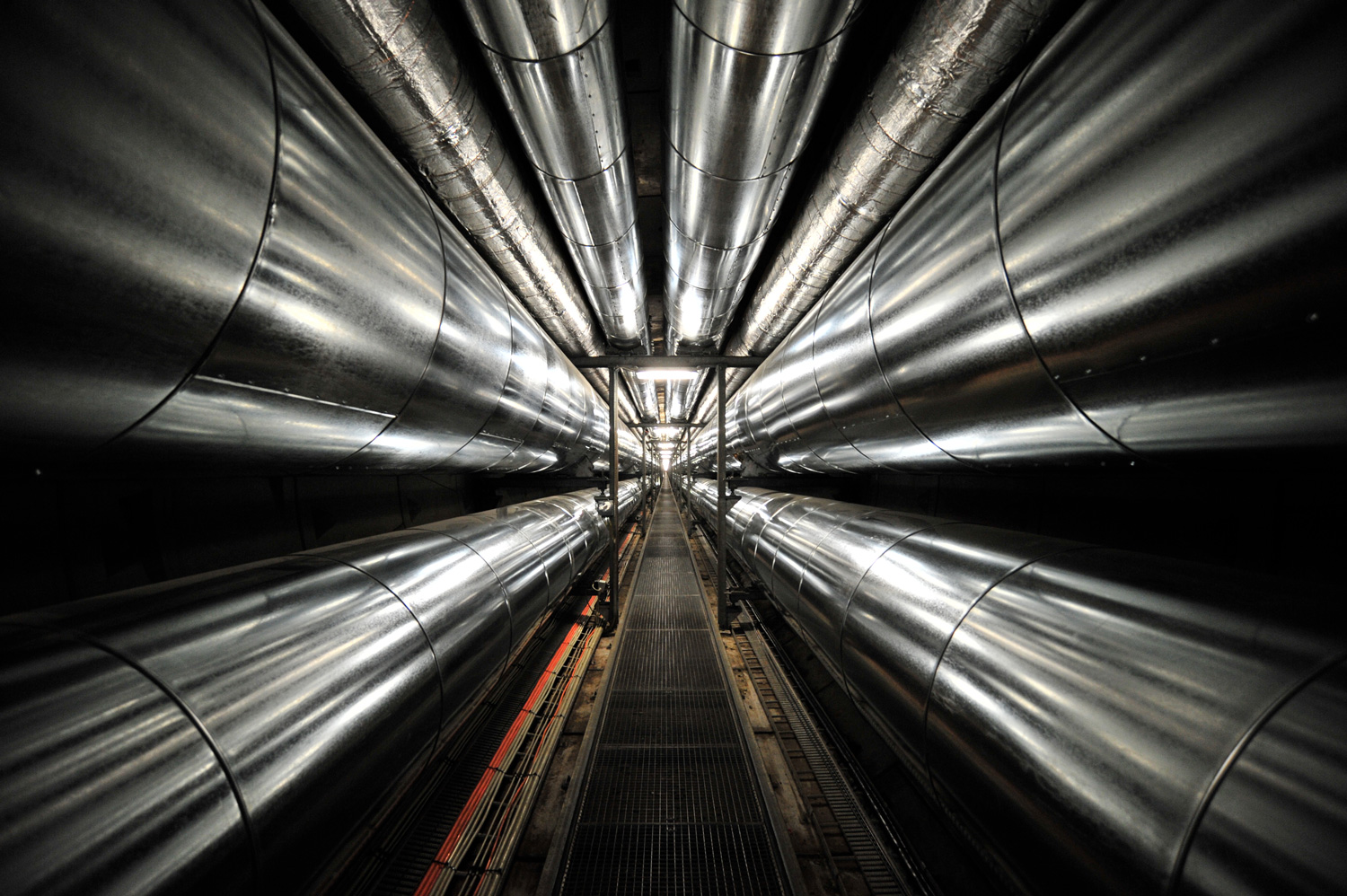
Cogeneration Plant Supervisory Control
A cogeneration plant is a system that allows the production of electricity and heat using a primary energy source, such as natural gas.
A Cogeneration Plant Supervisory Systems enables real-time control of plant operations and is essential to ensure energy efficiency and minimize operational costs. The supervisory system for cogeneration plants is designed to monitor all parameters of the plant, including temperature levels, pressure, humidity, and fuel consumption. This way, plant’s performance can be verified and optimized to achieve maximum energy efficiency.
Thanks to the cogeneration plant supervisory systems designed and developed by SIDeA, it is possible to remotely monitor the plant through a secure Internet connection.
Cogeneration Plant Supervisory Control
A cogeneration plant is a system that allows the production of electricity and heat using a primary energy source, such as natural gas.
A Cogeneration Plant Supervisory Systems enables real-time control of plant operations and is essential to ensure energy efficiency and minimize operational costs. The supervisory system for cogeneration plants is designed to monitor all parameters of the plant, including temperature levels, pressure, humidity, and fuel consumption. This way, plant’s performance can be verified and optimized to achieve maximum energy efficiency.
Thanks to the cogeneration plant supervisory systems designed and developed by SIDeA, it is possible to remotely monitor the plant through a secure Internet connection.
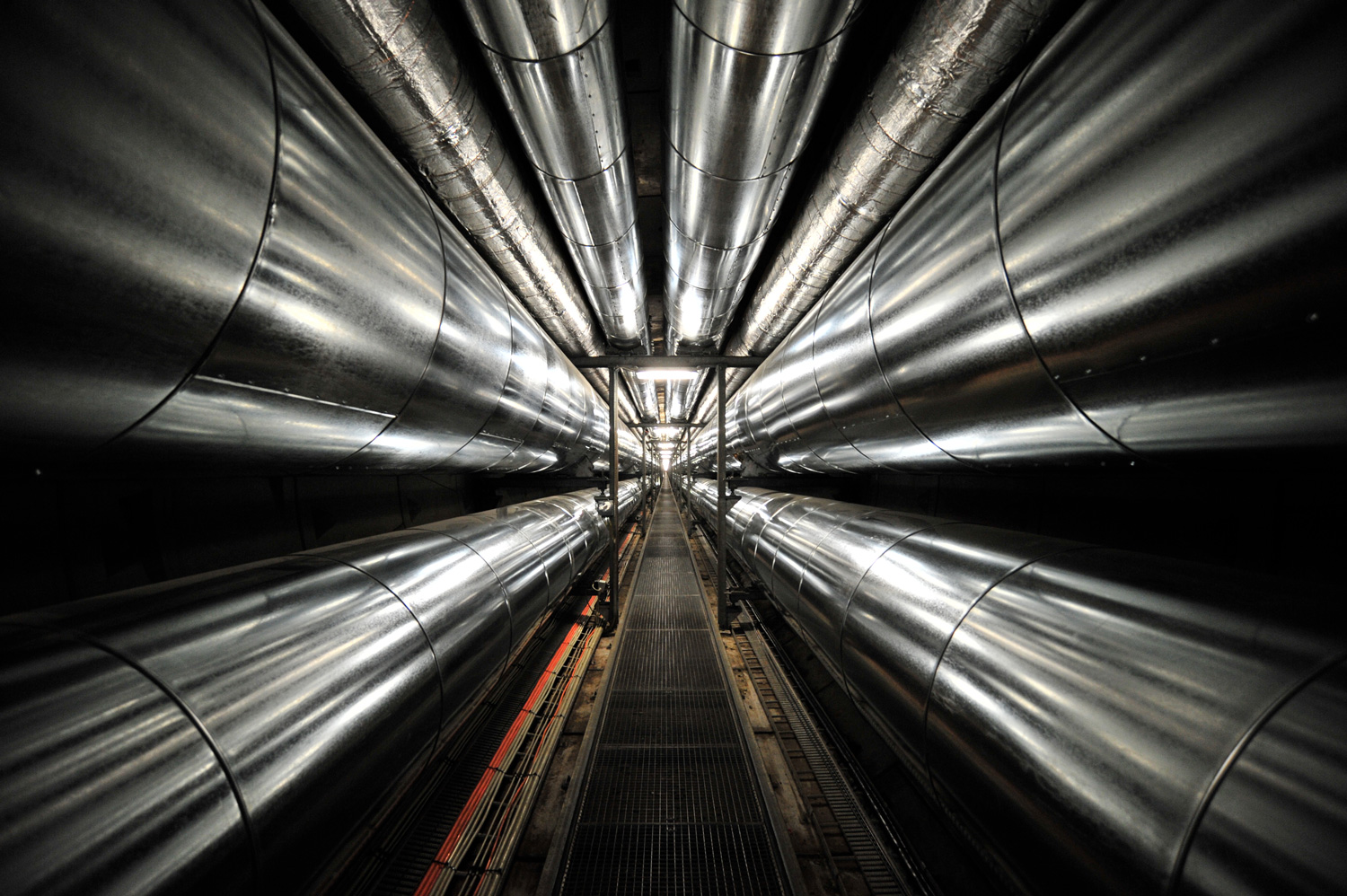
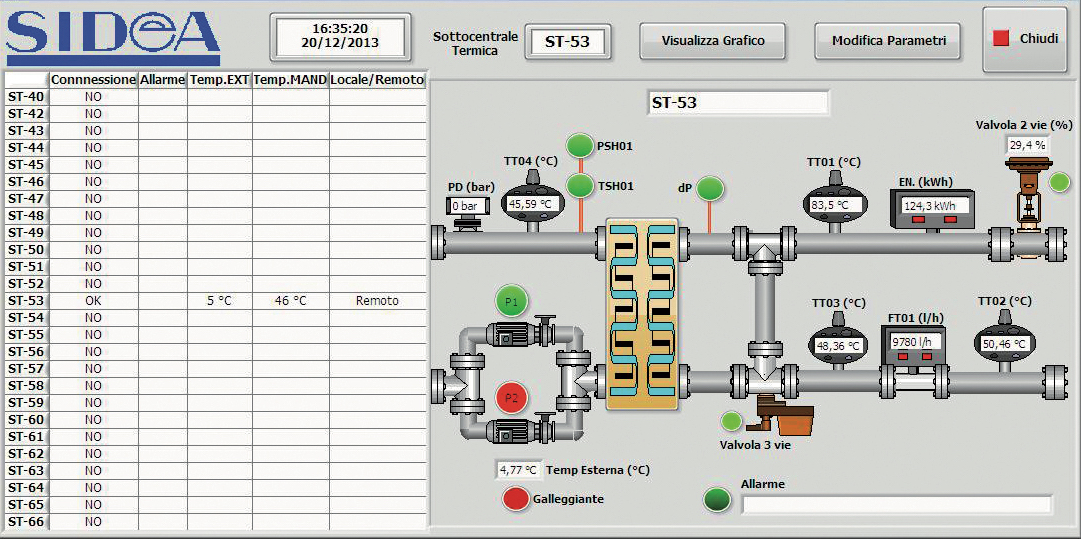
District Heating Plants Supervisory Control
A district heating plant is a thermal distribution system that provides heat to residential, commercial, or industrial buildings through a network of thermally insulated pipelines. Energy, generated centrally from sources such as thermal power plants, cogeneration facilities, or renewable sources, is transported via a heat transfer fluid (usually hot water or steam) through the pipelines to the end-users, where it is used for heating and producing domestic hot water.
The Kyoto Protocol identifies district heating as one of the most effective tools for reducing carbon dioxide emissions. Today, the latest European and national regulations already acknowledge its validity, obligating new constructions located less than a kilometer from a district heating network to design and prepare their systems to be supplied with heat from the distributed network (Directive 2002/91/EC, transposed by Legislative Decree 192/05 and subsequent amendments).
SIDeA designs and implements supervisory systems for district heating plants, taking care of the development and supply of all components that collaborate to monitor and control plant operations, including sensors, actuators, control units, supervisory software, and user interfaces.
The sensors detect key variables of the plant, such as temperature, pressure, flow, and energy consumption. These data are sent to the control units, which process the information and activate the actuators to regulate heat production and distribution to end-users. The supervisory software provided by SIDeA allows real-time data visualization and monitoring, report generation, alarm setting, and maintenance management through user interfaces that provide operators with an intuitive interaction with the district heating plant’s supervisory system.
Power Quality Monitoring
A power quality monitoring system measures and analyzes electrical power parameters and characteristics in order to evaluate and monitor power quality. This system is able to detect anomalies, disturbances and variations in voltage, current and other electrical parameters such as harmonics, voltage swings and power outages.
The power monitoring system records and analyzes measurement data to identify potential problems or malfunctions, providing valuable information for power quality improvement, fault prevention, process optimization and energy savings. Electrical quality monitoring results are usually presented through reports, graphs or dashboards for easy understanding.
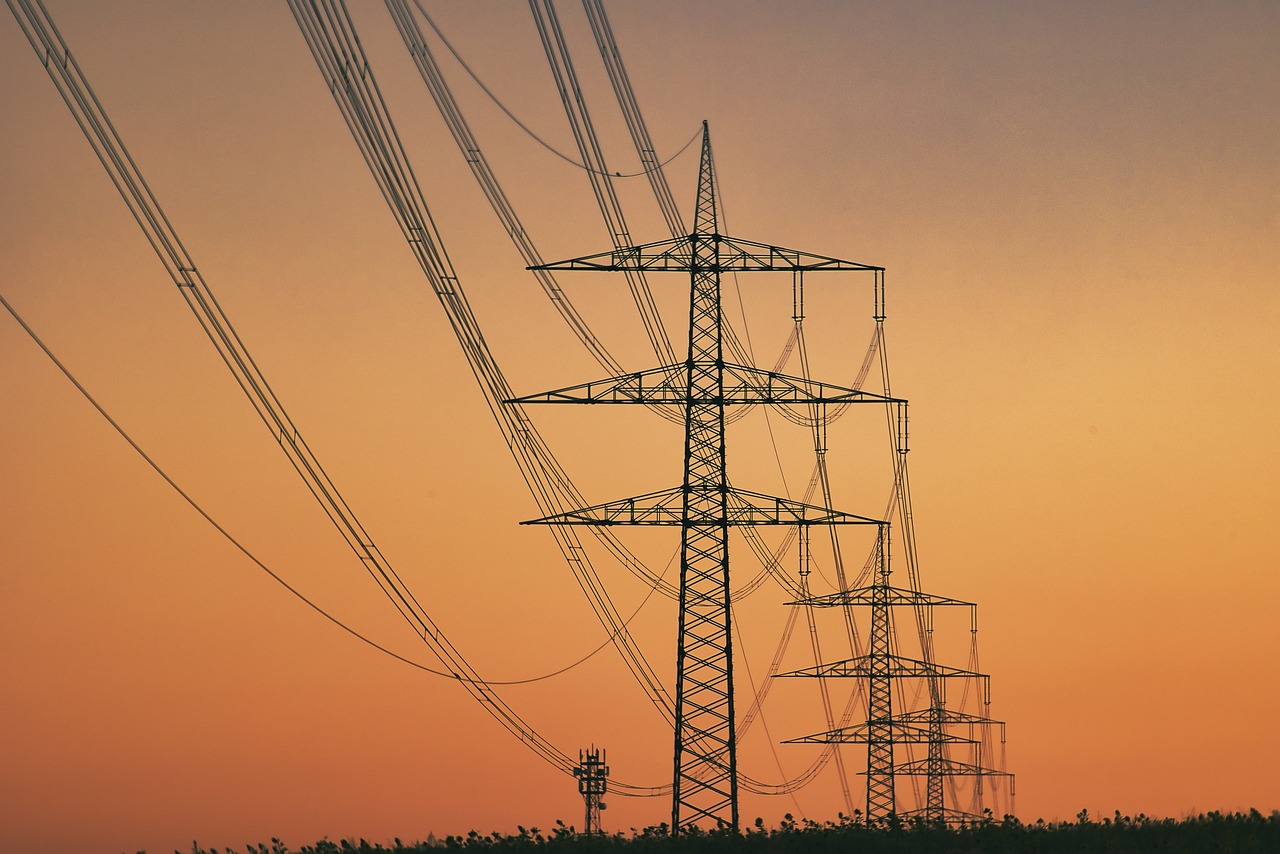
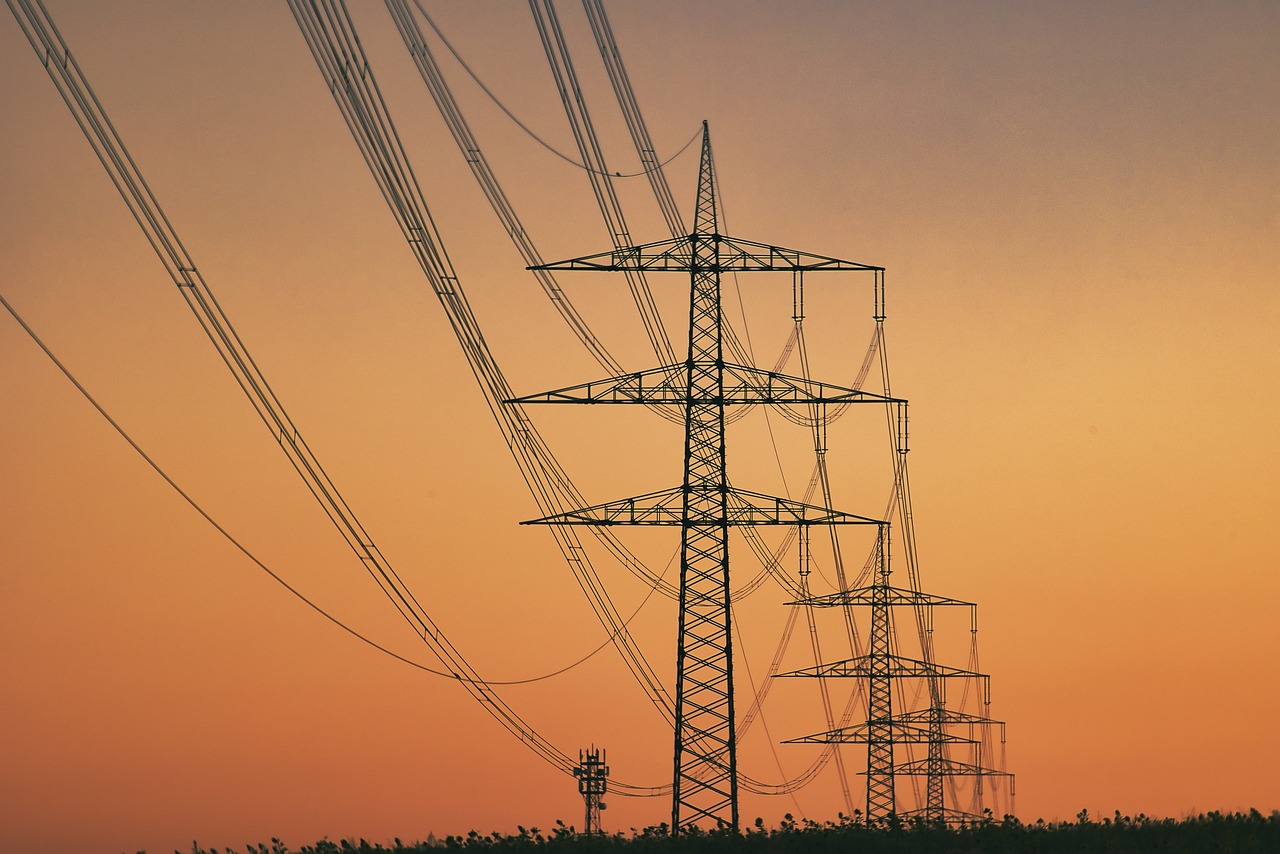
Power Quality Monitoring
A power quality monitoring system measures and analyzes electrical power parameters and characteristics in order to evaluate and monitor power quality. This system is able to detect anomalies, disturbances and variations in voltage, current and other electrical parameters such as harmonics, voltage swings and power outages.
The power monitoring system records and analyzes measurement data to identify potential problems or malfunctions, providing valuable information for power quality improvement, fault prevention, process optimization and energy savings. Electrical quality monitoring results are usually presented through reports, graphs or dashboards for easy understanding.